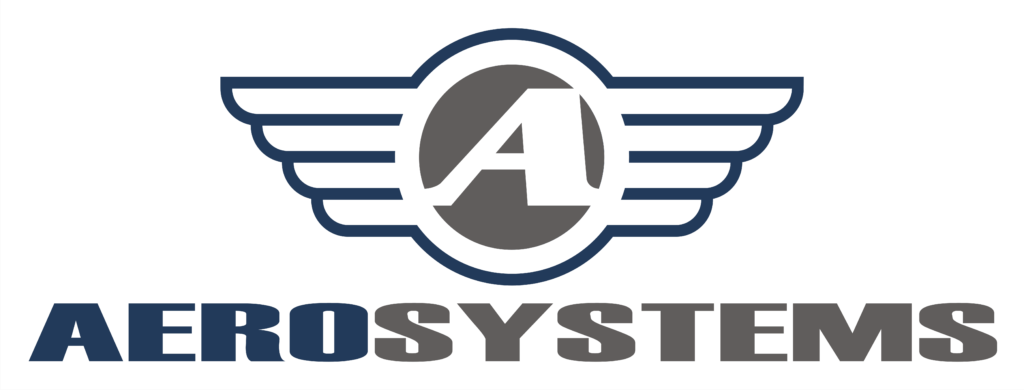
MISSION
Customer Satisfaction and Exceeding Customer Expectations through the creation of electro-mechanical components for the aerospace industry.
VISION
Aerosystems intends to assume a prominent place on the international market in the design, manufacturing and mantaiance of innovative electro-mechanical components for the aerospace industry, proposing itself as a Production and Services Company able to meet the ever growing needs of the major international aerospace industries.
QUALITY POLICY
The Integrated Policy complies with the following standards:
UNI EN ISO 9001:2015 – UNI EN 9100:2018 – UNI EN ISO 14001:2015.
For the biennium 2024-2025, Management is committed to maintaining the UNI EN ISO 9001:2015, EN 9100:2018, EASA Part 21, and EASA Part 145 certifications, extending the relevant Capability Lists (LOA), certifying the Environmental Management System in accordance with UNI EN ISO 14001:2015, and ensuring compliance with all mandatory requirements.
The continuous improvement of Products and the Integrated Management System is the top priority, achievable through the Corporate Improvement Plan based on the following Guidelines:
- Continuous improvement of the product and the system requires the involvement and participation of all personnel at every level. The primary motivation must be “CUSTOMER AND STAKEHOLDER SATISFACTION” and “EXCEEDING CUSTOMER EXPECTATIONS”.
- Each manager must create conditions for their team members to understand and implement the company’s quality policy and contribute to the CONTINUOUS IMPROVEMENT of company and environmental performance.
- TRAINING AND EDUCATION activities on quality and environmental topics must be precise and ongoing, covering all personnel.
- Based on an understanding of Customer needs, stakeholder requirements, and benchmarking against top competitors, and in line with the Company’s strategy, Management periodically defines PRIORITY OBJECTIVES to focus on.
The Objectives are established in the Strategy Plan and are as follows:
Contract Assignment: Creation of New Products to increase the Capability List
Customer Experience: Continuous improvement of the Customer Experience
LMS: Implementation of a consolidated training system – Learning Management System
ENVIRONMENT:Comply with the requirements of the Environmental Management System as specified by UNI EN ISO 14001:2015
Management has established that the Integrated Policy shall undergo periodic review to assess its adequacy and alignment with the expectations and requirements of customers, stakeholders, and mandatory standards (product, workplace health and safety, and environmental). Topics related to the adequacy review of the policy are included in the Management Review.
The Company has chosen to adopt a conduct focused on closely monitoring the level of service provided to Customers and stakeholders, viewing this not merely as the issuance of a certificate but, above all, as assistance and transparency in communication with Client Companies. Management requests the fullest collaboration from all personnel in maintaining Certifications by implementing all prescribed documents within the Corporate Management System and reporting any potential improvements to the respective managers.
AEROSYSTEMS – October 2024
FF16 Issue C – AS Quality Policy 2024